Düsseldorf, 18.08.2021 • Es ist ein weltweit verbreitetes Verfahren der Kunststoffverarbeitung: Bei der Produktion von Folien, Rohren oder Fensterprofilen wird Kunststoff durch einen Extruder aufgeschmolzen und in Form gepresst. Eine Innovation aus dem Rhein-Sieg-Kreis soll künftig bis zu 50 Prozent der dafür benötigten Heizenergie einsparen und den Ausschuss deutlich reduzieren. Das Projekt der Inmex GmbH wird durch das Sonderprogramm Umweltwirtschaft des NRW-Umweltministeriums gefördert und zusammen mit der Dr. Reinold Hagen Stiftung durchgeführt.
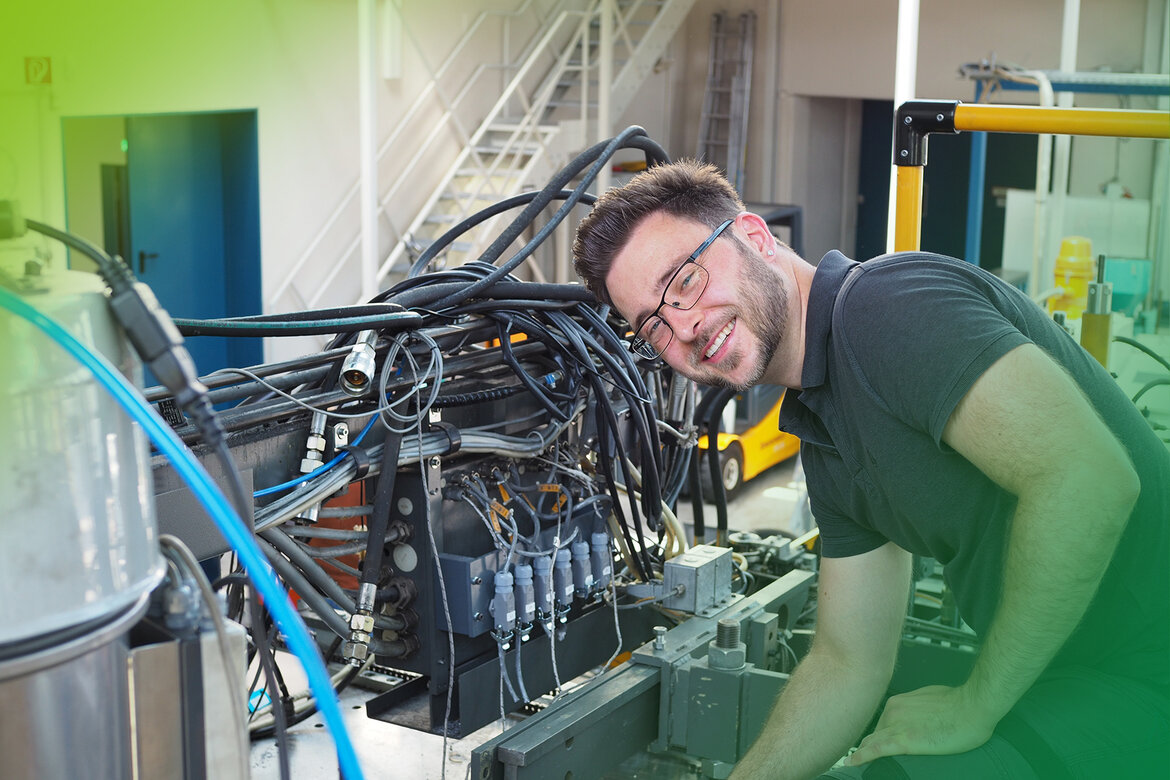
Manchmal muss man nur ein wenig genauer hinschauen, um zu erkennen, wo man etwas besser machen kann. Das gilt häufig besonders dann, wenn etwas schon sehr lange sehr gut funktioniert hat. Oft hilft der Blick von außen, um zu sehen: Innovation ist immer möglich. Was zählt, ist die richtige Idee – und die braucht manchmal auch die richtige Zeit.
Als etwa 1845 die ersten Pressen nach Art der archimedischen Schraube eingesetzt wurden, um eine plastische Masse unter Wärmeeinfluss technisch in Form zu bringen, dachte noch niemand an Energie- und Ressourceneffizienz oder den globalen Klimawandel. Und obwohl die zugehörigen Maschinen stetig weiterentwickelt wurden und ihre Antriebe und Steuerungssysteme heute Hightech darstellen, hat sich am Grundprinzip der Kunststoff-Extrusion seit rund 175 Jahren wenig geändert: Eine Schneckenpresse treibt in einem beheizten Zylinder eine Kunststoffmasse voran, bis diese die richtige Temperatur und Konsistenz erreicht hat, um am Ende durch einen Düsenkopf in Form gebracht zu werden. Auf diese Weise entstehen Kunststoffteile in endlosen Strängen, etwa Stäbe, Rohre oder Profile, Dichtungen oder auch Folien.
„Das Herzstück jedes Extruders ist ein temperierter Zylinder. Den möchten wir gerne zuverlässiger und besser temperieren. Dadurch erhalten wir einen stabileren Produktionsprozess mit weniger Ausschuss und sparen Energie“, beschreibt Axel Ifland, Geschäftsführer der Inmex GmbH aus Sankt Augustin. Der scheinbar simple Ansatz verfolgt klare Ziele: „Wir wollen den Heizwärmebedarf um die Hälfte senken und den Ausschuss um ein Viertel.“
Ein endloser Produktionsprozess
Die Kunststoff-Extrusion ist ein kontinuierlicher Produktionsprozess: Einmal gestartet läuft dieser im Prinzip immer gleichförmig weiter. Vorne wird fortwährend Rohmaterial aufgenommen, idealerweise in Form von recyceltem oder bio-basiertem Kunststoff-Granulat. Am Ende wächst ein vorgeformter Materialstrang heraus, der in nachgelagerten Schritten zumeist noch weiter bearbeitet wird. Um diesen endlosen Ausstoß zu ermöglichen, zielt die Konstruktion darauf ab, dass die Kunststoffmasse an der Austrittsdüse kontinuierlich mit verlässlicher Konsistenz, Temperatur und gleichmäßigem Druck ankommt. Im Inneren des Extruders wird der Kunststoff dazu erwärmt und durch die Schnecke vorangetrieben. Weil dieser Vorgang Reibungswärme verursacht, muss die Kunststoffmasse auf dem Weg durch den Extruder abschnittweise jedoch wieder gekühlt werden. „Es gibt verschiedene Zonen, die oft abwechselnd geheizt und gekühlt werden. Alles, um die Temperatur im Innern auf dem exakt richtigen Wert zu halten“, erläutert Ifland. Um dies zu gewährleisten, sind im Extruder in regelmäßigen Abständen Messfühler sowie Heiz- und Kühlvorrichtungen angebracht. Es gilt, ein empfindliches Gleichgewicht zu halten, um optimal zu produzieren. „Wenn dabei etwas nicht stimmt, dann produziert die Maschine Ausschuss. Das können schnell mehrere hundert Meter werden, die aufwendig recycelt werden müssen.“
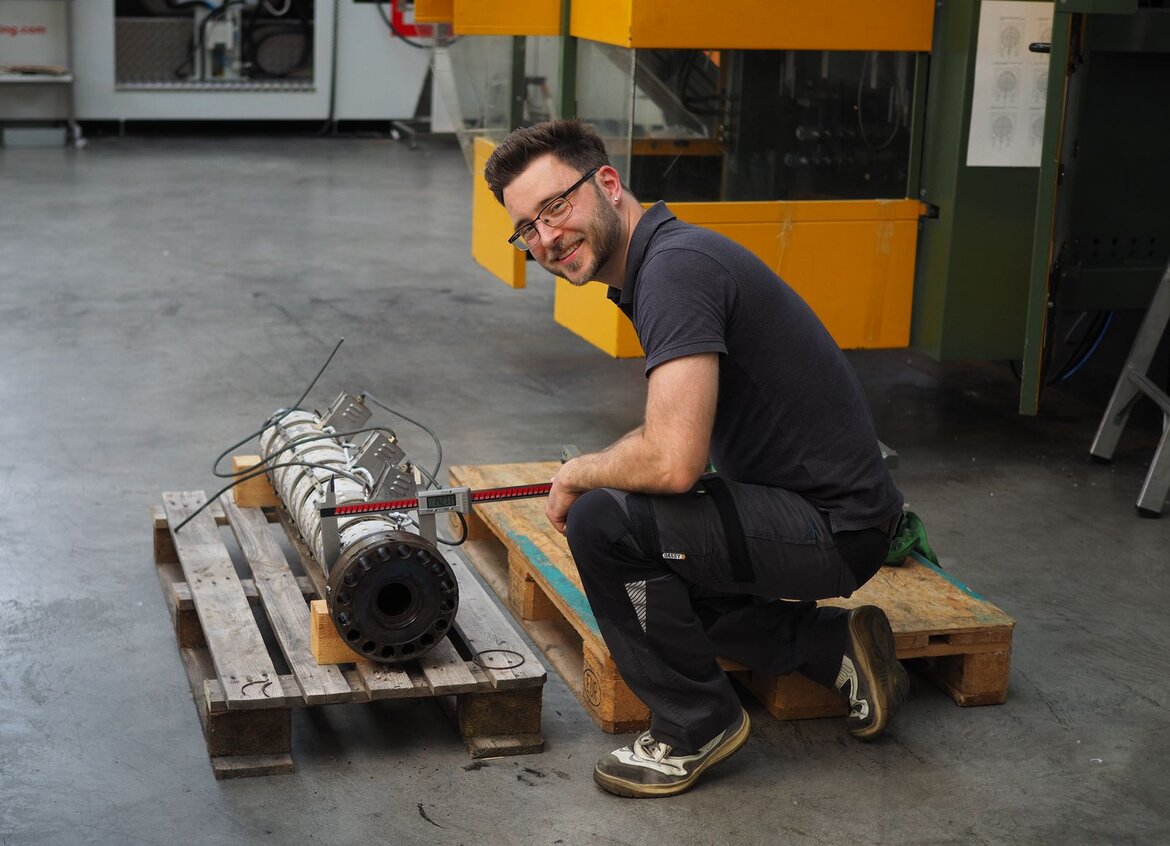
Ein eingespieltes Verfahren besser machen
Man kann sich leicht vorstellen, dass der stete Wechsel zwischen Heizen und Kühlen nicht besonders energieeffizient ist. Um diesen Prozess zu optimieren, hat sich das Team von Inmex die entsprechenden Heiz- und Kühlvorrichtungen genau angeschaut. Wie sich zeigte, arbeiten diese indirekt und dadurch träge. Denn geheizt wird in der Regel von außen, mittels halbschalenförmiger Heizbänder, die den Zylinder umschließen. Die Kühlung besorgen Lüfter, die ebenfalls von außen Raumluft auf den Extruder blasen. „Um das Heizband herum ist ein Blechgehäuse mit dem Lüfter. Und wenn innen der Kunststoff gekühlt werden muss, bläst dieser von außen das Heizband an. Das ist aktuell Stand der Technik.“
Eine direkte und damit effizientere Heiz- und Kühlmöglichkeit im Inneren des Extruders verspricht demgegenüber einen deutlichen Fortschritt. Dazu sollen ein längliches Heizelement und ein Kühlrohr spiralförmig in das Metall des Extruderzylinders eingebettet werden. „Beide sind über Dreiviertel ihrer Oberfläche direkt mit dem Zylinder verbunden und können damit schneller Wärme oder Kühlung in den Zylinder bringen. Und weil beides in den Zylinder integriert ist, kann das Ganze von außen mit einer Wärmeisolation umgeben werden. So lassen sich weitere Energieverluste vermeiden“, beschreibt Ifland das neue Prinzip.
Energieeffizienz zum Nachrüsten
Als mögliches Produkt steht am Ende ein Nachrüstsatz für bestehende Extrusionsmaschinen diverser Hersteller und Bauarten, so dass die Kunststoff-Verarbeiter mit überschaubarer Investition schrittweise umrüsten können. Ein Patent für die Technologie wurde schon beantragt. „Das Zylinderrohr eines Extruders muss von Zeit zu Zeit aufgearbeitet oder getauscht werden. Das wäre ein guter Zeitpunkt, um unser System nachzurüsten. Je nachdem, welche Einsparungen wir erreichen, kann es sich aber auch lohnen, allein aus diesem Grund sofort umzusteigen“, lautet Iflands Fazit.
Im Rahmen der Förderung durch das Sonderprogramm Umweltwirtschaft soll die Konstruktion weiter entwickelt und als Prototyp realisiert werden. Dazu werden zu Beginn des Projektes gezielt aus mehreren Produktionsvorgängen die relevanten Daten erhoben und später mit der erreichten Effizienzsteigerung abgeglichen. Unterstützt wird das Team der Inmex dabei durch den auf Verfahrenstechnik spezialisieren Projektpartner Dr. Reinold Hagen Stiftung in Bonn, der auch eine Testanlage zur Verfügung stellt.
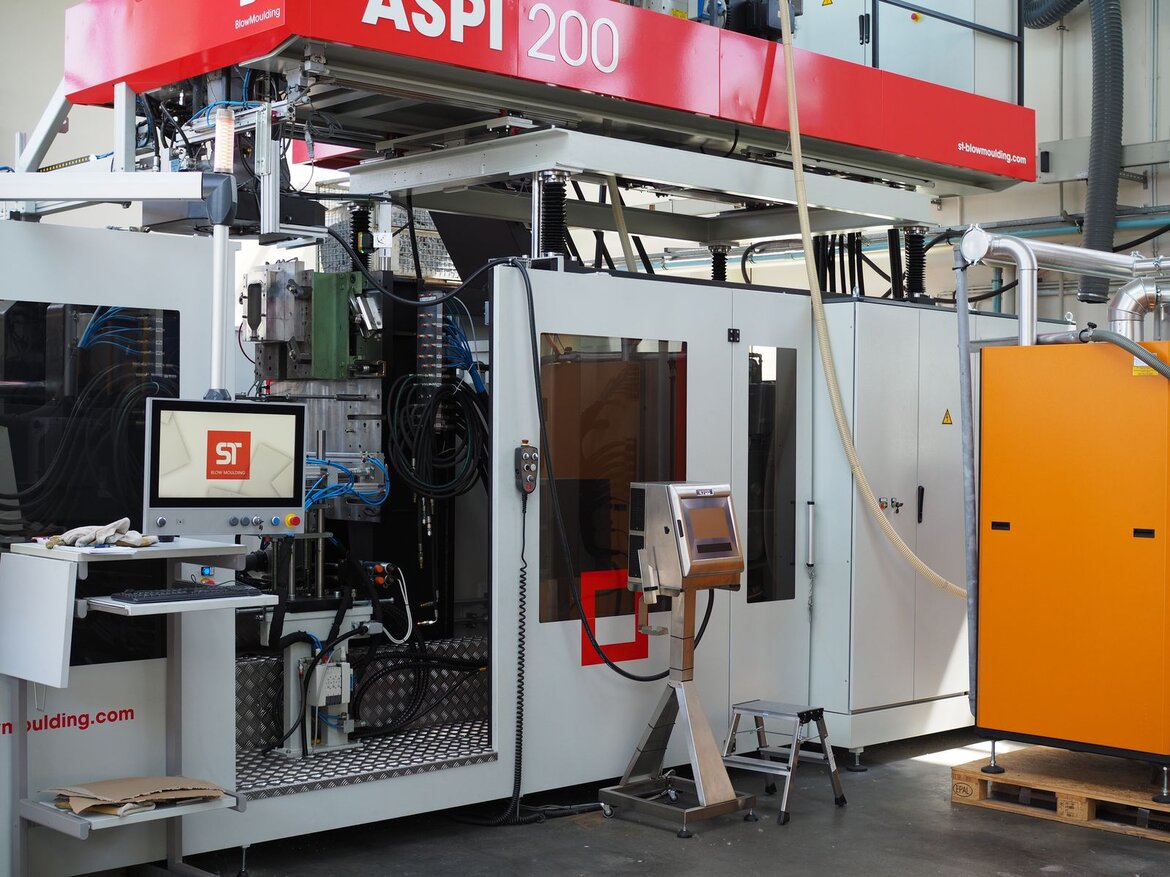
Ein grünes Geschäftsmodell aus NRW
„Wir sind ein grünes Unternehmen“, sagt Ifland über die Inmex GmbH. Und in der Tat wäre es nicht das erste Mal, dass es ihnen gelingt, einen etablierten Produktionsprozess energiesparend und ressourcenschonender zu gestalten. Das Unternehmen wurde vor drei Jahren als Ausgründung der Hochschule Bonn-Rhein-Sieg gegründet, um eine ganz ähnliche Idee für das Kunststoff-Spritzgießverfahren an den Markt zu bringen. Auch hier ging es um das Thema Energieeffizienz, das den Maschinenbauer Ifland schon seit seinem Studium begleitet. Die damals entstandene energieeffiziente Plastifiziereinheit bildet heute das Kernprodukt der Rheinländer und erfreut sich einer starken Nachfrage. Auch dieses wird im Übrigen als Retrofit für alle erdenklichen Maschinentypen angeboten.
Wenn es nach den Vorstellungen des Unternehmensgründers geht, könnte mit der neuen Produktidee durchaus an diesen Erfolg angeknüpft werden: „Die künftigen Marktchancen beurteilen wir als sehr gut. Allein in Europa werden jährlich geschätzt 30 Millionen Tonnen Kunststoff in der Extrusion verarbeitet und das Thema Energieeffizienz wird zunehmend wichtiger. Wir haben also noch große Pläne. Mittelfristig möchten wir weltweit agieren.“
***
Das Projekt „Extruder-Temperiersystem“ wird im Rahmen der Umweltwirtschaftsstrategie des Landes Nordrhein-Westfalen gefördert. Die als Nachrüstsatz entwickelte Technologie soll ein verbreitetes Verfahren in der Kunststoffverarbeitung energieeffizienter gestalten und den Produktionsausschuss deutlich reduzieren. Umweltwirtschaft – Vorsprung für NRW.