Düsseldorf/Rösrath, 08.11.2023 • Alu ist nicht gleich Alu. Um Altmetalle effizient wiederverwenden zu können, ist daher eine exakte Sortierung der Legierungen entscheidend. Die cleansort GmbH aus Rösrath liefert mit einem innovativen Laserverfahren eine Vollanalyse in Echtzeit und ermöglicht damit beim Aluminiumrecycling Energieeinsparungen von bis zu 95 Prozent.
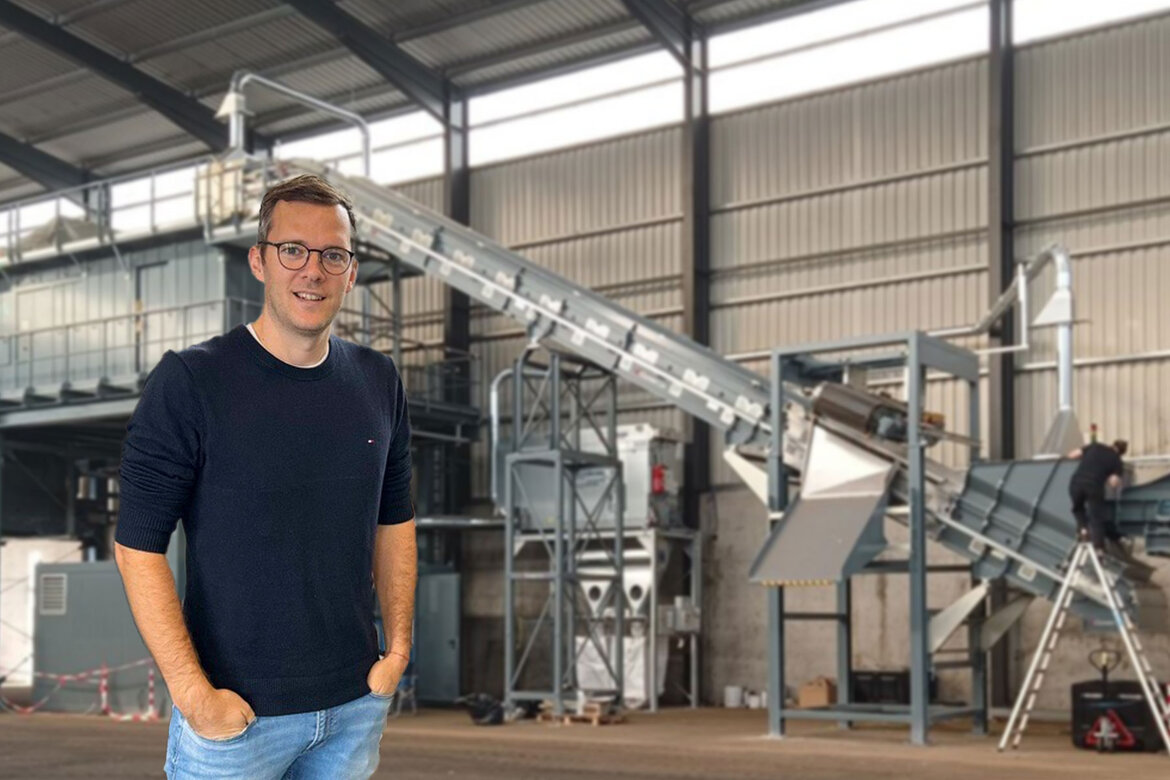
Laserstrahlen beflügeln seit Jahrzehnten die Phantasie, nicht nur in der Science Fiction. Die Erfindung geht auf den von Albert Einstein beschriebenen Photoeffekt zurück und hat es geschafft, bis heute immer neue Anwendungsfelder zu erobern und Innovationen hervorzubringen. Laser messen, schweißen, tasten DVD und Blu-Ray ab, ermöglichen Operationen an der Netzhaut und erfassen dreidimensionale Strukturen im Raum. Auch die Laserspektroskopie und die Laserablation sind heute bekannte Verfahren mit zahlreichen Einsatzgebieten. Das Rösrather Unternehmen cleansort hat sie innovativ in einer neuartigen Sortieranlage für Metalle kombiniert und will damit das Metallrecycling auf eine neue Stufe heben.
„Unsere Anlage sortiert im Zweischichtbetrieb ca. 30.000 Tonnen Aluminium pro Jahr und spart damit rund 291.000 Megawattstunden an Energie ein, das entspricht rund 130.000 Tonnen CO2“, sagt Philipp Soest, Mitgründer und geschäftsführender Gesellschafter des Unternehmens. „Die Grundlage dafür ist eine Echtzeitanalyse der Metalle, so dass wir unterschiedliche Legierungen voneinander trennen können.“
Um Metalle recyceln zu können, müssen sie zuvor sortiert werden. Bisher eingesetzte Sortieranlagen können dabei problemlos zwischen verschiedenen Metallen unterscheiden, beispielsweise zwischen Eisen bzw. Stahl und Aluminium. Dazu werden die durch die Anlage laufenden Metallteile per Röntgenanalyse durchleuchtet und anhand ihrer Dichteunterschiede sortiert. Natürlich wird in einer vielfältigen Industrie nicht nur Eisen und Aluminium verwendet. Stattdessen werden je nach Anwendungsfall aus individuellen Kombinationen verschiedener Metalle spezielle Legierungen mit jeweils eigenen Materialeigenschaften entwickelt. So fügt man dem reinen Aluminium beispielsweise Magnesium hinzu, um seine Korrosionsbeständigkeit zu steigern und es formbarer zu machen. Aluminiumlegierungen mit Zink erreichen dagegen hohe Festigkeitswerte. Insgesamt gibt es mittlerweile etwa 200 verschiede Aluminium-Legierungen. Beim Stahl sieht es ähnlich aus. Über 40 verschiedene Stahlsorten werden beispielsweise allein in einem Pkw eingesetzt.
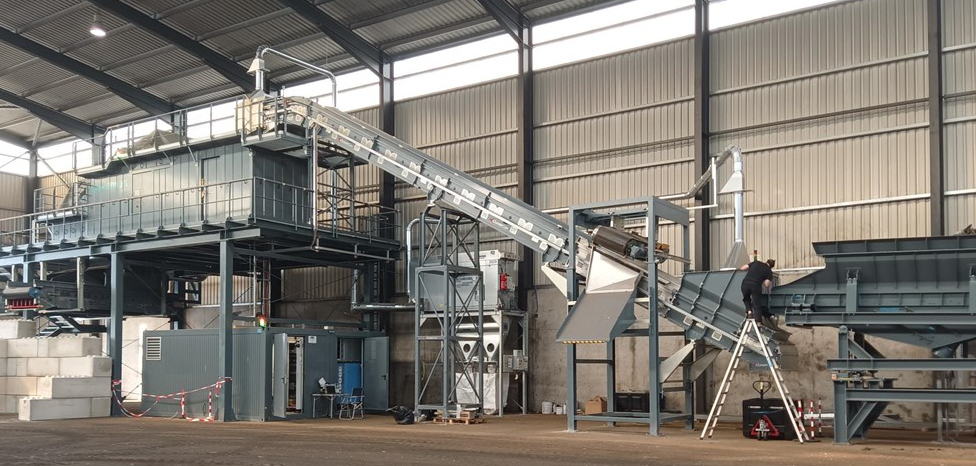
Mit elf Stundenkilometern in die Analyse
Die Vielzahl unterschiedlicher Legierungen bringt die herkömmliche Röntgenanalyse an ihre Grenzen: Sie kann Legierungen in der Regel nicht unterscheiden. Hier beginnt die Arbeit der cleansort. Philipp Soest beschreibt den Prozess so: „Bevor das Altmetall sortiert werden kann, wird es zerkleinert und dann kontinuierlich unserer Anlage zugeführt. Über ein Steigband und eine Schwingrinne werden die einzelnen Metallteile, einzelne Stücke oder Bleche zwischen 2 und 80 Zentimetern Kantenlänge, dann auf einem Förderband verteilt. Auf einer Breite von 1,20 Metern laufen die Einzelteile nun durch die Analyse. Dabei erreichen sie eine Geschwindigkeit von drei Metern pro Sekunde, das sind rund elf Stundenkilometer.“
Die Analyse ist das Herzstück der Anlage – und das Einsatzfeld der Lasertechnik. So entscheidend ist die Rolle der gebündelten Lichtstrahlen für diesen Prozess, es erinnert fast ein wenig an „Star Wars“: Zunächst erfasst ein Laserscanner die Position jedes einzelnen Metallteilchens auf dem Förderband. Bei der Laserablation – lateinisch für „Abtragung“ – wird nun auf jedem Teil eine Stelle zur Analyse vorbereitet, indem punktuell die obersten Materialschichten entfernt werden. „Lack- oder Zinkschichten, es kann alles Mögliche auf der Oberfläche sein. Auf einer winzigen Fläche von 0,3 mal 0,3 Millimetern wird deshalb das Grundmaterial freigelegt“, erklärt Soest. Ist die Fläche auf diese Weise vorbereitet, folgt die laserinduzierte Plasmaspektroskopie. Dazu wird auf jedem Analysepunkt Metall verdampft, bis ein Plasma entsteht. Beim Zerfall des Plasmas sendet es einen Lichtimpuls aus, der über eine Optik erfasst und dann analysiert wird. Das Ergebnis ist ein charakteristisches Profil der im Licht enthaltenen Wellenlängen; und es gibt Aufschluss über Art und Menge der in der Legierung enthaltenen Elemente. Mit jedem Durchlauf kann die Anlage zwei vorgegebene Metalllegierungen exakt voneinander trennen, die nach Kundenwunsch konfiguriert werden.
„Die Anlage erfasst und analysiert nahezu jedes einzelne Metallstück auf dem Förderband. Pro Teil benötigen wir dafür 6,4 Millisekunden. So sortieren wir derzeit über 2 Kilogramm pro Sekunde bzw. rund acht Tonnen Aluminium pro Stunde“, sagt der gelernte Maschinenbauer Soest, „Diese hohe Sortiergeschwindigkeit ist das entscheidende Kriterium für die Wirtschaftlichkeit.
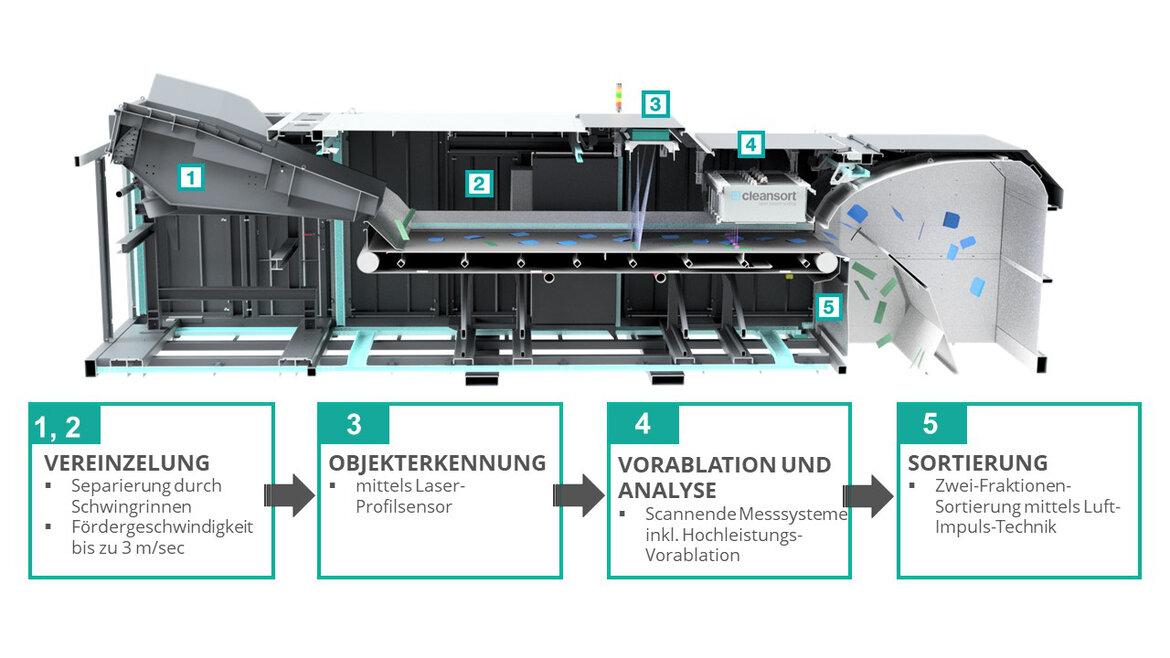
Aus Neu wird Neu – und spart Energie
Wirtschaftlichkeit verspricht am Ende auch die hohe Energieeinsparung, die durch ein derart sortenreines Recycling möglich wird. Und diese entsteht zum Beispiel so: Um eine marktfähige Legierung herzustellen, muss Rohaluminium im exakten Mischverhältnis mit den entsprechenden Elementen versetzt werden. Recyceltes Aluminium besteht aber heute in der Regel aus verschiedenen miteinander vermischten Legierungen. Es kann daher nicht wie Rohaluminium verwendet, sondern diesem nur begrenzt beigemischt werden. Höchstens ein Drittel darf der Anteil an recyceltem Aluminium sein, wenn daraus wieder hochwertige Rohstoffe entstehen sollen. Wenngleich also der Recyclinganteil von Aluminium schon heute bei nahezu 100 Prozent steht, ist immer wieder neues Rohaluminium nötig, um den Kreislauf im Gang zu halten. Und dessen Produktion ist extrem energieintensiv und, aufgrund der hohen Strompreise, gerade in Deutschland auch sehr teuer. „Mit unserer Sortiertechnologie kann man Aluminium- und Stahllegierungen direkt im Kreislauf fahren, wir brauchen also nicht immer neue Rohstoffe und sparen bis zu 95 Prozent der benötigten Energie ein. Wir führen dazu gerade mit verschiedenen Partnern ein Forschungsprojekt durch, das die ganze Wertschöpfungskette in der Automobilbranche abdeckt. Wir zeigen darin, wie aus dem Lenkrad wieder ein Lenkrad und aus der Felge wieder eine Felge werden kann“, sagt Soest.
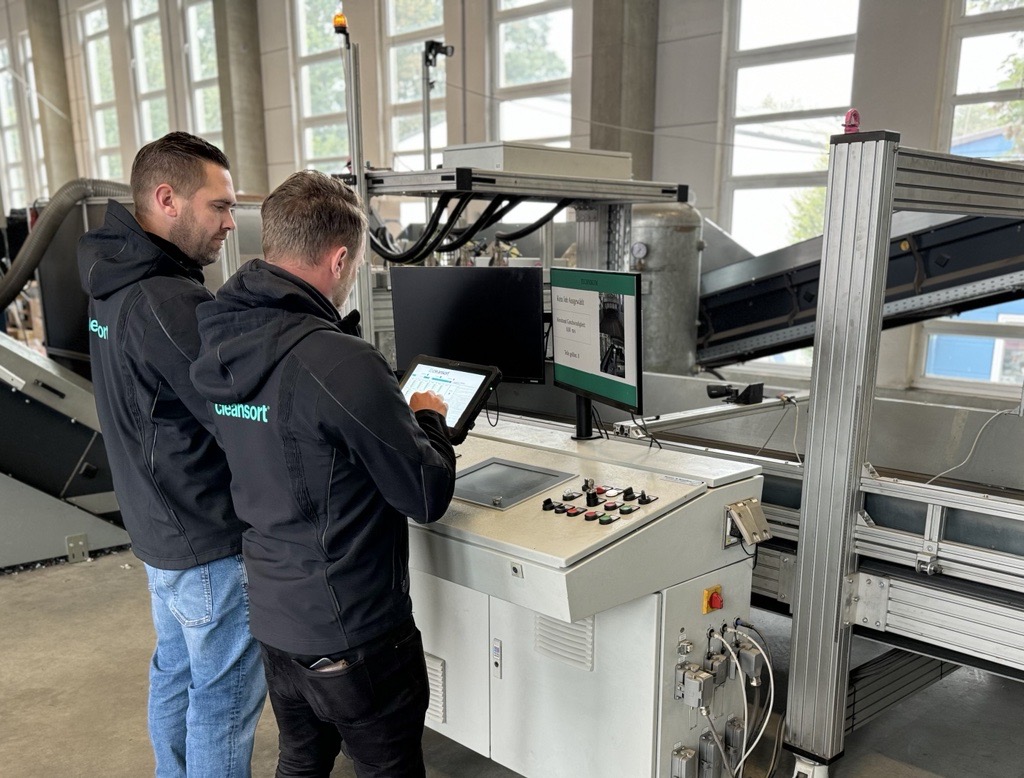
Von Rösrath in die Welt
Das Unternehmen cleansort wurde 2018 gegründet und kann, nachdem in den ersten Jahren im Wesentlichen die Technologie entwickelt wurde, heute zwei erfolgreich installierte Sortieranlagen bei Kunden in Deutschland vorweisen. Beide laufen im regulären kommerziellen Betrieb. Und weitere Anlagen sollen alsbald folgen. „2024 werden wir den Umsatz etwa verfünffachen und uns personell verdoppeln. Und im Jahr darauf wollen wir dann weltweit unsere Anlagen anbieten. Wir sind auf dem Weg in eine Kreislaufwirtschaft. Der Bedarf ist da – und gut für die Umwelt ist es außerdem.“
***
Die cleansort GmbH liefert Metallsortieranlagen, die mittels laserinduzierter Plasmaspektroskopie zwischen verschiedenen Metalllegierungen unterscheiden und dabei rund acht Tonnen Altmetall in der Stunde sortieren können. Die Sortierung ermöglicht ein sortenreies Recycling mit hoher Energieeinsparung. Green Economy – stark in NRW.